U Tube Bundle Heat Exchanger
U-tube Heat Exchanger is a common configuration used in thermal management. As the name suggests, it comprises a bundle of tubes bent into a U-shape, typically housed within a shell. The design facilitates the exchange of heat between two fluids, ensuring efficient energy transfer without direct contact between them. This fundamental principle serves as the foundation for the diverse applications of U-tube heat exchangers across industries.. U tube heat exchanger is composed of some main components like the tube box, shell, and tube buddle. What’s more, it is easy to drying after the U tube heat exchanger hydrotest.
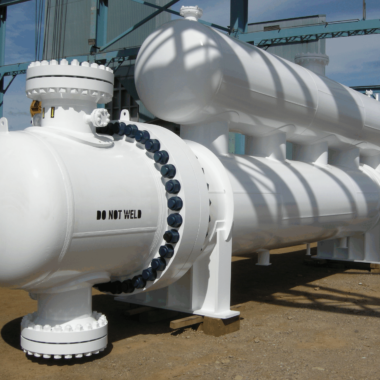
Advantages U Tube Heat Exchanger
- The tube bundle can expand or contract freely, preventing thermal stress due to temperature differences between the tube and shell, providing good thermal compensation performance.
- The structure is simple, with only one tube sheet and fewer sealing surfaces, making it cost-effective.
- It is easy to clean and maintain the U-tube heat exchanger, as the tube bundle can be removed from the shell body.
- This heat exchanger is lightweight and suitable for high-temperature and high-pressure applications.
Different Parts of a U-Tube Heat Exchanger
- Tubes:
The heart of the U-tube heat exchanger, these tubes constitute the primary components for heat exchange. Constructed from materials tailored to withstand corrosive environments and high temperatures, they ensure prolonged operational durability.
- Shell:
Surrounding the tube bundle, the shell provides structural support and containment for the fluid streams. Its design varies depending on factors like pressure, temperature, and fluid properties, with options ranging from cylindrical to rectangular configurations.
- Tube Sheets:
Positioned at both ends of the tube bundle, tube sheets serve as crucial interfaces, securing the tubes in place while facilitating fluid ingress and egress. Their robust construction is paramount for maintaining structural integrity under operational conditions.
- Headers:
These components connect the tubes to the inlet and outlet piping, enabling seamless integration within the larger system. Headers play an important role in ensuring uniform flow distribution and minimising pressure drop across the heat exchanger.
- Baffles:
Strategically placed within the shell, baffles optimise fluid flow patterns to maximise turbulence and enhance heat transfer efficiency. Their geometric configuration and spacing are designed to mitigate flow stagnation and promote uniform distribution.
- Support Structures:
Integral to the overall stability of the U-tube heat exchanger, support structures provide mechanical reinforcement and alignment for the tube bundle and other components. Proper installation and maintenance of these structures are imperative for long-term reliability.
Different Parts of Bundle Heat Exchanger
- Efficiency:
The U-tube design maximises heat transfer efficiency by promoting turbulence and optimising the temperature gradient between the process and utility fluids. This results in higher rates of heat exchange and improved thermal performance compared to other heat exchanger configurations.
- Compact Design:
U-tube heat exchangers offer a compact footprint, making them ideal for installations where space is limited. Their efficient design minimises the required floor area without compromising performance, allowing businesses to optimise their use of available space in industrial facilities.
- Enhanced Heat Transfer:
The U-shaped tube configuration induces turbulence in the fluid flow, which enhances heat transfer rates by disrupting boundary layers and promoting better mixing between the process and utility fluids. This results in improved heat exchange efficiency and higher thermal performance compared to straight-tube counterparts.
- Versatility
U-tube heat exchangers are versatile solutions that can be customised to meet the specific requirements of various industrial applications. Whether used for heating, cooling, condensing, or evaporating processes, they can accommodate different fluid types, flow rates, and operating conditions, making them suitable for a wide range of industries and applications.
- Reduced Maintenance:
The self-cleaning action of turbulent flow within the heat exchangers helps prevent fouling and reduces the need for frequent maintenance interventions. This results in lower maintenance costs and prolonged operational uptime for businesses, contributing to overall cost savings and improved reliability of industrial systems.
- Cost-Effectiveness:
U-tube heat exchangers offer a cost-effective solution for thermal management needs, providing efficient heat transfer performance at competitive prices. Their high thermal efficiency, long operational lifespan, and reduced maintenance requirements contribute to lower operating costs and improved return on investment for businesses.
- High Durability:
Constructed from high-quality materials such as stainless steel or titanium, U-tube heat exchangers exhibit excellent corrosion resistance and mechanical strength, ensuring long-term durability and reliability in demanding industrial environments. This durability reduces the risk of premature failure and downtime, allowing businesses to maintain consistent productivity and operational efficiency.
- Easy Installation:
They are designed for easy installation and integration into existing systems, minimising downtime and installation costs for businesses. Their straightforward design and standardised components simplify the installation process, allowing businesses to quickly deploy and commission these heat exchangers in industrial facilities.
Application of Heat Exchanger
- HVAC Systems:
U-tube heat exchangers play a vital role in heating, ventilation, and air conditioning (HVAC) systems for commercial and industrial buildings. They facilitate the exchange of heat between indoor and outdoor air, ensuring optimal temperature control and energy efficiency.
- Power Generation:
In power plants, they are used in various processes, including steam generation, condensation, and turbine cooling. They help maximise thermal efficiency and maintain operational stability in power generation facilities.
- Oil Refining:
U-tube heat exchangers are integral to the refining of crude oil into various petroleum products. They facilitate heat transfer in processes such as distillation, catalytic cracking, and desalting, contributing to the production of high-quality fuels and lubricants.
- Chemical Processing:
The chemical industry relies on these heat exchangers for heating, cooling, and condensing processes in the production of chemicals and petrochemicals. They enable precise temperature control and efficient energy utilisation in chemical reaction vessels and distillation columns.
- Metal Processing:
U-tube heat exchangers are utilised in metal processing applications such as heat treatment, annealing, and quenching. They help regulate temperatures during various metallurgical processes, ensuring the desired mechanical properties and quality of metal products.
- Sterilisation:
U-tube heat exchangers are employed in pharmaceutical manufacturing facilities for sterilising liquids, equipment, and packaging materials. They play a critical role in ensuring product safety and compliance with stringent regulatory standards.
- Drug Manufacturing:
These heat exchangers facilitate precise temperature control in pharmaceutical processes such as crystallisation, drying, and evaporation. They contribute to the efficient production of pharmaceutical formulations while maintaining product integrity and consistency.
- Cleanroom Environments:
HVAC systems equipped with U-tube heat exchangers are essential for maintaining cleanroom environments in pharmaceutical facilities. They help control temperature and humidity levels to ensure optimal conditions for drug manufacturing and storage.
- Reaction Cooling:
The heat exchangers are used in chemical reactors to remove heat generated during exothermic reactions. They prevent overheating and facilitate efficient heat dissipation, allowing for precise control of reaction kinetics and product quality.
- Solvent Recovery:
In chemical processing plants, U-tube heat exchangers are crucial in solvent recovery systems. They facilitate the condensation of vapours emitted during solvent evaporation processes, enabling the recovery and reuse of valuable chemicals.
- Distillation:
These tubes are employed in distillation columns for separating chemical components based on their boiling points. They facilitate heat exchange between the ascending vapour and descending liquid streams, contributing to the efficient fractionation of chemical mixtures.
- Pasteurisation:
U-tube heat exchangers are utilised in the food industry for pasteurising milk, juices, and other beverages. They heat the product to a specific temperature for a predetermined time, effectively destroying harmful pathogens while preserving flavour and nutritional quality.
- Food Processing:
They are employed in various food processing applications, including cooking, blanching, and sterilisation. They help maintain precise temperature control and ensure uniform heating or cooling of food products, enhancing safety and shelf life.
- Brewing and Distilling:
In breweries and distilleries, U-tube heat exchangers are critical in the mashing, fermentation, and distillation processes. They facilitate the efficient transfer of heat between different stages of production, contributing to the quality and consistency of alcoholic beverages.
- Wastewater Treatment:
U-tube heat exchangers are utilised in wastewater treatment plants for various thermal processes, including sludge digestion, anaerobic digestion, and thermal hydrolysis. They help optimise the treatment efficiency and energy recovery from wastewater streams.
- Geothermal Heating:
They are integral components of geothermal heating and cooling systems. They facilitate the exchange of heat between the underground geothermal reservoir and the circulating fluid, providing sustainable and efficient heating or cooling for residential and commercial buildings.
- Renewable Energy:
U-tube heat exchangers play a role in renewable energy systems such as solar thermal power plants and biomass facilities. They contribute to the efficient conversion of solar or biomass energy into heat, which can be utilised for electricity generation or heating applications.