Air Cooled Heat Exchanger
Air Cooled Heat Exchanger are used to cool and or condense process streams with ambient air as the cooling medium rather than water. Cooling with air is often economically advantageous, e.g., in arid or semi-arid locations, in areas where the available water requires extensive treatment to reduce fouling, or when additional investment would otherwise be required to expand a plant’s existing cooling-water supply. Regulations governing water use and discharge of effluent streams to the environment also tend to favour air cooling.
Air cooled heat exchangers are used to transfer heat from a process fluid to ambient air. The process fluid is contained within heat conducting tubes. Atmospheric air, which serves as the coolant, is caused to flow perpendicularly across the tubes in order to remove heat. In a typical air-cooled heat exchanger, the ambient air is either forced or induced by a fan or fans to flow vertically across a horizontal section of tubes. For condensing applications, the bundle may be sloped or vertical. Similarly, for relatively small air-cooled heat exchanger, the air flow may be horizontal across vertical tube bundles.
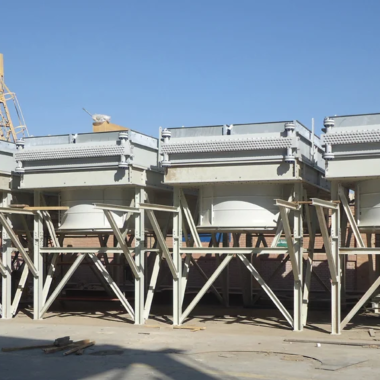
Types of Air Cooled Heat Exchanger
- Forced Draught Type Air-Cooled Heat Exchanger
- Induced Draught Type Air-Cooled Heat Exchanger
Advantages of Induced Draft Air Cooled Heat Exchanger
- Better distribution of air across the bundle.
- Less possibility of the hot effluent air recirculating around to the intake of the sections. The hot air is discharged upward at approximately 2.5 times the velocity of intake, or about 1500 ft/min.
- Better process control and stability because the plenum covers 60% of the bundle face area, reducing the effects of sun, rain, and hail.
- Increased capacity in the event of fan failure, since the natural draft stack effect is much greater with induced draft.
Advantages of Forced Draft
- Slightly lower horsepower since the fan is in cold air (horsepower varies directly as the absolute temperature).
- Better accessibility of fans and upper bearings for maintenance.
- Easily adaptable for warm air recirculation in cold climates.
- Better accessibility of bundles for replacement.
- Accommodates higher process inlet temperatures.
Industries Used Air Cooled Heat Exchanger
- Cement
- Chemical
- Commercial & Real Estate
- EPC (Engineering, Procurement, and Construction)
- Pharmaceutical
- Power
- Refinery
- Sponge Iron
- Steel
Application
- Gas/Air Compressor Coolers
- Gas Transmission Coolers
- Engine & Generator Coolers
- Air Cooled Condensers
- Steam Condensers
- Lube Oil Cooling Systems
- Flue Gas Reactors
- CNG Booster Compressor Cooler
- Data Centre Cooling System