
Manufacturer Glycol Chiller
Manufacturer Glycol Chiller
Manufacturer Glycol chiller are closed-loop systems. The coolant circulates continuously without coming into contact with the outside world. Since the system is sealed, there is no water loss from evaporation and the glycol coolant stays clean, uncontaminated, And does not create fouling or scaling. A closed-loop system is incredibly effective and durable.
Closed-loop systems are less expensive to build since they require less pumping power. Through tubing attached to the input and output parts of the chiller, the glycol coolant is pumped.
Heat Exchangers – Evaporator
The glycol water coolant and the refrigerant gas can exchange heat thanks to the heat exchanger. The heat from the refrigerant is captured and transferred away from the region being cooled using the flowing glycol. Due to the fact that glycol can remove more heat, the heat exchanger and glycol pipelines are small.
Glycol Chiller Pump
The fundamental factor preventing the use of high-powered pumps to run a glycol chiller is the low viscosity of glycol. Although modest, glycol system pumps are a crucial component of the system. They aid in keeping the temperature consistently cold and in circulating the glycol. The cooling system may need more than one pump, depending on the layout of the chiller unit and the type of application.
Compressor of Glycol Chiller
The compressor converts low pressure, low temperature refrigerant to high pressure, high temperature. There are various types of compressors include centrifugal, diaphragm, screw, positive displacement, and screw types.
Condenser of Glycol chiller
The condenser gathers the surplus heat that the evaporator and compressor transferred to it from the chiller and condenser, respectively. The water then transfers the heat into the condenser’s surrounding area. After that, the heat is discharged into the surrounding air.
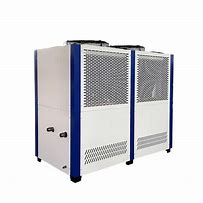
Manufacturer Glycol Chiller