HYDRAULIC OIL CHILLER
During production, the hydraulic oil occasionally warms up. However, as the oil warms up, its properties change, rendering it unusable for the procedure. Therefore, controlling the oil’s temperature is crucial for lengthening its shelf life and the related machinery. This is done using hydraulic chillers, which are typically attached to the oil supply directly or have pumps. Through the chiller circuit, hot oil is pumped to change the temperature. In order to transfer heat from a cold source into a liquid or gas, these chillers use fluid dynamics.
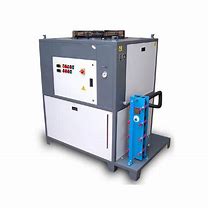
hydraulic oil chiller
TECHNIQUES TO BE FOLLOWED TO COOL OIL CHILLER
- To assist in cooling the heated oil, a water/glycol coolant has been fitted. Either a chiller is used directly or an installed coolant is used to cool the hydraulic fluid.
- As a result, hydraulic oil heats the glycol/water coolant.
KEY FEATURES
- Quite effective yet more prone.
- Has a significant cooling potential, even in areas with high air temperatures.
- Make use of a sophisticated “H-smart” microprocessor-based controller.
- drives that have the ability to change frequency.
- Steel serves as the body.
- The protocol interface for BMS Compressor safety controllers for equipment is relatively simple.
- Switches are a helpful lubricant for managing water flow and antifreeze safety.
We are also the best manufacturer of hydraulic heat exchangers. Lubricating and quenching oils, as well as heat transfer fluids, can all be used with these oil coolers. They are premium goods that use the greatest components and most recent technological advancements. The tube stack is completely floatable, which reduces thermal strains and makes it simple to remove should cleaning be required.
Get the best product to your Industry/Home at Coolfab Equipments