Forced draft cooling tower -Tamilnadu
Forced draft cooling tower -Tamilnadu A cooling tower in which the fan is installed on the side of the tower to allow air to flow from the bottom to upward of the tower is called a forced draft cooling tower. This is one of the most economical and powerful cooling towers used in different industrial plants.
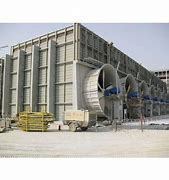
Forced draft cooling tower -Tamilnadu
The forced draft cooling towers remove low-potential heat generated in the production process. They use atmospheric cooling with wet technology and forced draft. A counterflow of air and hot water in the cooling fill results in a heat transfer.
There are many benefits of using a forced draft cooling tower. And that is exactly why so many industrial plants opt for this model over the other options. Forced draft cooling towers are very powerful and affordable at the same time. These models will remove low-potential heat that is generated in the production process. A counterflow of air combined with hot water results in a transfer of heat in the cooling fill. Paper and chemical industry plants often prefer to used forced draft cooling tower.
Forced Draft Cooling Tower Components
Here is a look at all of the components making up a forced draft cooling tower:
- Fan stack.
- Fan with drive.
- Cooling fill.
- Drift eliminators.
- Outer shell.
- Water basin.
- Water distribution system.
Forced Draft Features
- Ease of maintenance.
- Lower noise levels.
- Dry air stream drive.
- Low-absorbed capacity.
The forced draft cooling towers remove low-potential heat generated in the production process. For heat exchangers using cooling water, if there is an internal leak in one of the tubes or the tube sheet and the working pressure is higher than the cooling water pressure, the combustible product will enter the cooling water. This combustible product mixes with the cooling water and then enters the cooling tower, where it vaporizes and, in some cases, ignites.
Therefore, if you have a heat exchanger with cooling water, it must have less pressure on the process side than the waterside. In such a case, if leakage still occurs there, water will go into the process stream. This is generally less dangerous than the case of hydrocarbons getting into the cooling water.