Direct and Indirect-Heat Exchanger
Direct and Indirect-Heat Exchanger Indirect contact heat exchangers keep the fluids exchanging heat separate by the use of tubes or plates etc.. Direct contact exchangers do not separate the fluids exchanging heat and in fact rely on the fluids being in close contact.
Another heat transfer technology is the fluid bed. This technology works well when a precise control of temperature and residence time is required such as in polymer, chemical and pharmaceutical industries. Fluid beds force air through perforated steel beds that fluidizes free flowing bulk solids. As material is added to one end of the fluidized bed, it moves gradually from one end of the bed to the other. Air or gases are introduced in this process, moving between the material particles, removing the moisture and changing the final temperature. Air has two functions in fluid bed technology; first it creates the fluidized state of the material enabling the product to flow and second, it either heats or dries the material through direct contact.
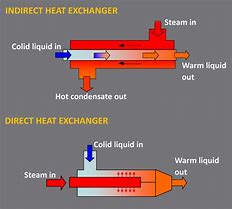
Direct and Indirect-Heat Exchanger
Quite simply, direct heating technology involves a bulk solid material coming into direct contact with a heating gas to change the final temperature of the material. On the other hand, indirect heating technology does not allow the product to come in contact with air or gas or any other heating agent to change the final temperature. Indirect heat transfer uses conduction, radiation or convection to achieve temperature change. There are various types of technologies used in both the direct and indirect heating of bulk solids.
ROTARY DRUM DIRECT HEAT TRANSFER
Rotary drums are commonly used to remove moisture content from a free flowing bulk solid, by bringing the material in direct contact with a heated gas, commonly air. A rotary drum is a cylindrical tube, that slopes slightly downwards and rotates rapidly. As the product (ex. powder, fertilizer, sugar) enters the drum dryer, the rotating mechanism lifts the material up onto a series of internal fins lining the inner walls of the dryer. As the material flows toward the discharge end, it falls off the fins and passes through the hot gas stream within the rotary drum, removing moisture. The gas flowing through the drum can flow in either a co-current or counter-current direction.
ROTARY DRUM INDIRECT HEAT TRANSFER
Rotary drums can also be used in niche applications as an indirect heat transfer mechanism. This works especially well with fine, lightweight materials or highly combustible materials. The indirect heat transfer process relies on the heat from the drum’s shell to dry or heat the material through conduction and radiation. The product does not come in direct contact with air in this process. To achieve conduction, hot water is poured over the drum as it rotates, heating the outer shell and in turn the material inside.